धातु उत्पादों को अनुकूलित करते समय, उत्पाद की गुणवत्ता, लागत और वितरण समय के लिए सही प्रसंस्करण विधि का चयन करना महत्वपूर्ण है। धातुओं को अनुकूलित करने के लिए विभिन्न सामान्य तरीके हैं।यहां आमतौर पर उपयोग की जाने वाली कई धातु अनुकूलन विधियां दी गई हैं:
1.सीएनसी मशीनिंग:
सीएनसी (कंप्यूटर न्यूमेरिकल कंट्रोल) मशीनिंग कंप्यूटर-नियंत्रित मशीन टूल्स का उपयोग करके सटीक धातु काटने और प्रसंस्करण की एक विधि है।पूर्व-क्रमादेशित निर्देशों का उपयोग करके, सीएनसी मशीनिंग धातु भागों के उच्च-परिशुद्धता और कुशल अनुकूलन को सक्षम बनाती है, जो जटिल आकार और सटीक आवश्यकताओं वाले उत्पादों के लिए उपयुक्त है।
लाभ:
उच्च परिशुद्धता और सटीकता
संगत सामग्रियों की विस्तृत श्रृंखला
जटिल आकृतियों और जटिल डिज़ाइनों के लिए उपयुक्त
छोटे और बड़े उत्पादन दोनों के लिए कुशल
नुकसान:
प्रारंभिक सेटअप लागत अधिक
जटिल डिज़ाइनों के लिए लंबा उत्पादन समय
घटिया निर्माण (सामग्री हटाना) तक सीमित
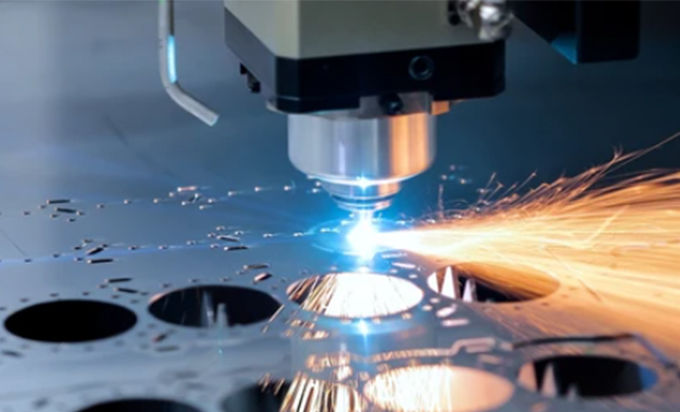
2. मिलिंग और टर्निंग:
मिलिंग और टर्निंग में अनुकूलित आकार और आकार प्राप्त करने के लिए मशीनिंग उपकरण पर उपकरणों का उपयोग करके वर्कपीस से धातु सामग्री को काटना शामिल है।मिलिंग सपाट और जटिल सतह मशीनिंग के लिए उपयुक्त है, जबकि टर्निंग का उपयोग बेलनाकार वर्कपीस के लिए किया जाता है।
लाभ:
सटीक और सटीक मशीनिंग
विभिन्न आकृतियों और आकारों के लिए बहुमुखी
प्रोटोटाइप और बड़े पैमाने पर उत्पादन दोनों के लिए उपयुक्त
संगत सामग्रियों की विस्तृत श्रृंखला
नुकसान:
जटिल डिज़ाइनों के लिए मशीनिंग का लंबा समय
उच्च उपकरण और रखरखाव लागत
मोड़ने में घूर्णी या सममित भागों तक सीमित
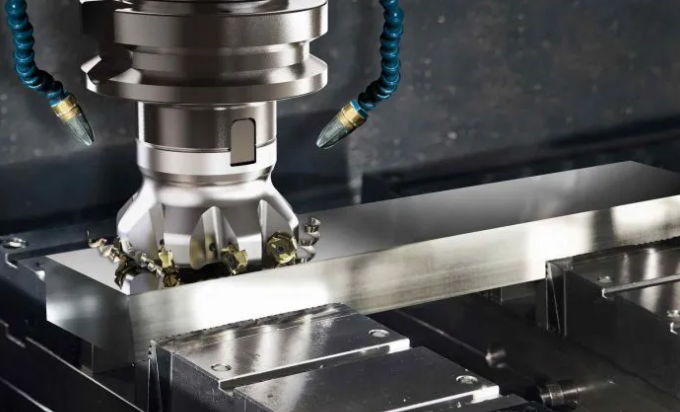
3.3 डी प्रिंटिग:
3डी प्रिंटिंग तकनीक सामग्री के परत-दर-परत जमाव द्वारा धातु भागों के अनुकूलन को सक्षम बनाती है।धातु के पाउडर को पिघलाकर या ठोस बनाकर, जटिल आकार के धातु भागों को सीधे मुद्रित किया जा सकता है, जिससे गति, लचीलेपन और अनुकूलन के लाभ मिलते हैं।
लाभ:
अत्यधिक अनुकूलन योग्य और जटिल डिज़ाइन
तीव्र प्रोटोटाइपिंग और कम लीड समय
पारंपरिक तरीकों की तुलना में कम सामग्री बर्बादी
कम मात्रा में उत्पादन के लिए उपयुक्त
नुकसान:
पारंपरिक तरीकों की तुलना में सीमित सामग्री विकल्प
कुछ पारंपरिक तरीकों की तुलना में कम ताकत और स्थायित्व
बड़े हिस्सों के लिए धीमी उत्पादन गति
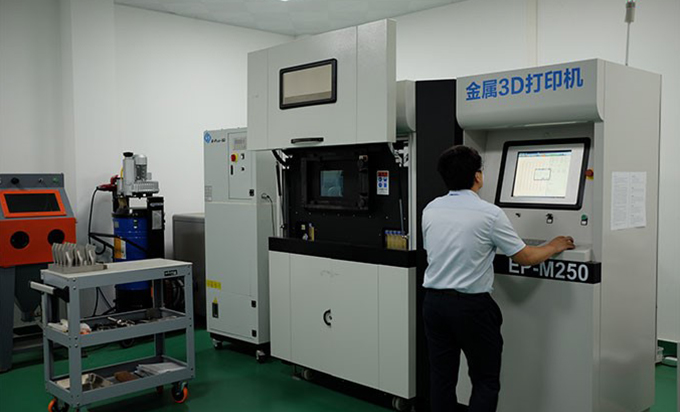
4.लेजर कटिंग:
लेज़र कटिंग एक ऐसी विधि है जो काटने के प्रयोजनों के लिए धातु सामग्री को पिघलाने, वाष्पीकृत करने या जलाने के लिए उच्च-ऊर्जा लेज़र बीम का उपयोग करती है।लेजर कटिंग उच्च परिशुद्धता, गति, गैर-संपर्क और न्यूनतम विरूपण जैसे लाभ प्रदान करती है, जो इसे धातु भागों और संरचनाओं की एक विस्तृत श्रृंखला को अनुकूलित करने के लिए उपयुक्त बनाती है।
लाभ:
उच्च परिशुद्धता और बारीक विवरण
तेज काटने की गति
गैर-संपर्क प्रक्रिया, सामग्री विरूपण को कम करना
विभिन्न धातुओं और मोटाई के लिए उपयुक्त
नुकसान:
2डी कटिंग प्रोफाइल तक सीमित
उच्च उपकरण और रखरखाव लागत
चिकने किनारों के लिए अतिरिक्त पोस्ट-प्रोसेसिंग की आवश्यकता हो सकती है
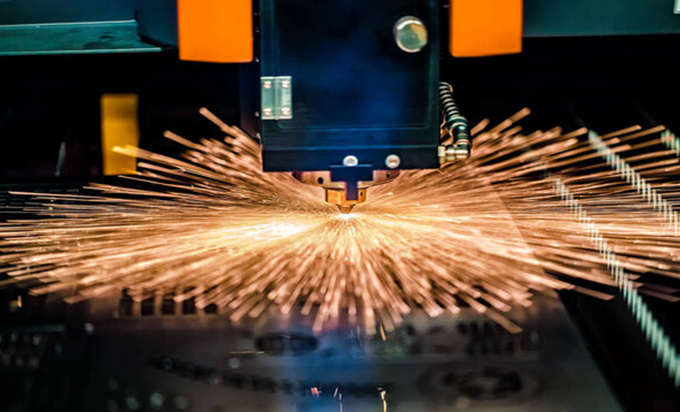
5.मुद्रांकनऔर गठन:
स्टैम्पिंग और फॉर्मिंग में धातु सामग्री को वांछित आकार देने के लिए उस पर दबाव डालना शामिल है।जटिल आकार और उच्च परिशुद्धता के साथ कस्टम धातु भागों और घटकों को प्राप्त करने के लिए कोल्ड स्टैम्पिंग या हॉट स्टैम्पिंग प्रक्रियाओं का उपयोग किया जा सकता है।
लाभ:
बड़ी मात्रा के लिए उच्च उत्पादन गति
दोहराए जाने वाले डिज़ाइनों के लिए लागत प्रभावी
जटिल आकृतियों और सख्त सहनशीलता के लिए उपयुक्त
बढ़ी हुई सामग्री की ताकत और स्थायित्व
नुकसान:
उच्च प्रारंभिक टूलींग लागत
विशिष्ट आकृतियों और आकारों तक सीमित
प्रोटोटाइप या छोटे प्रोडक्शन रन के लिए आदर्श नहीं है
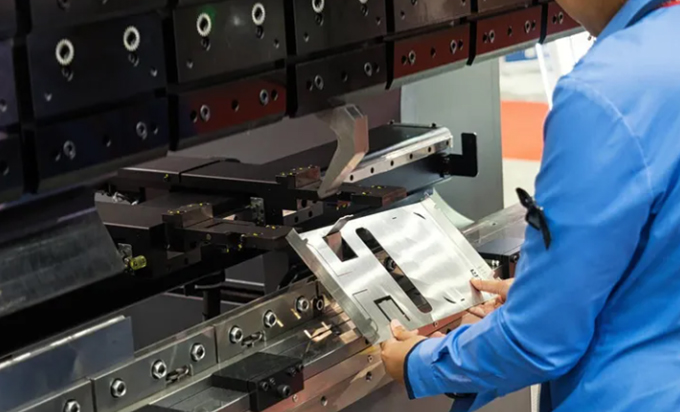
6.मेटल सांचों में ढालना:
डाई कास्टिंग एक ऐसी प्रक्रिया है जिसमें पिघली हुई धातु को तेजी से जमने और वांछित आकार बनाने के लिए उच्च दबाव के तहत एक सांचे में डाला जाता है।मुख्य चरणों में मोल्ड तैयार करना, धातु पिघलना, इंजेक्शन, ठंडा करना और डिमोल्डिंग शामिल हैं।
लाभ:
उच्च परिशुद्धता: डाई कास्टिंग जटिल आकार, जटिल विवरण और सटीक आयामों के साथ भागों का उत्पादन कर सकती है, जिससे स्थिरता और उच्च सटीकता सुनिश्चित होती है।
उच्च उत्पादन क्षमता: डाई कास्टिंग तेजी से इंजेक्शन और तेजी से शीतलन के साथ बड़े पैमाने पर उत्पादन के लिए उपयुक्त है, जिससे उच्च आउटपुट दर सक्षम होती है।
मजबूती और टिकाऊपन: डाई-कास्ट हिस्से आम तौर पर उच्च शक्ति, कठोरता और संक्षारण प्रतिरोध सहित उत्कृष्ट यांत्रिक गुणों का प्रदर्शन करते हैं।
नुकसान:
उच्च लागत: डाई कास्टिंग के लिए समर्पित धातु मोल्ड के उत्पादन की आवश्यकता होती है, जो मोल्ड निर्माण और तैयारी लागत के मामले में महंगा हो सकता है।
सीमित सामग्री चयन: डाई कास्टिंग मुख्य रूप से कम पिघलने बिंदु वाली धातुओं जैसे एल्यूमीनियम मिश्र धातु, जस्ता मिश्र धातु और मैग्नीशियम मिश्र धातु पर लागू होती है।यह स्टील या तांबे जैसी उच्च गलनांक वाली धातुओं के लिए कम उपयुक्त है।
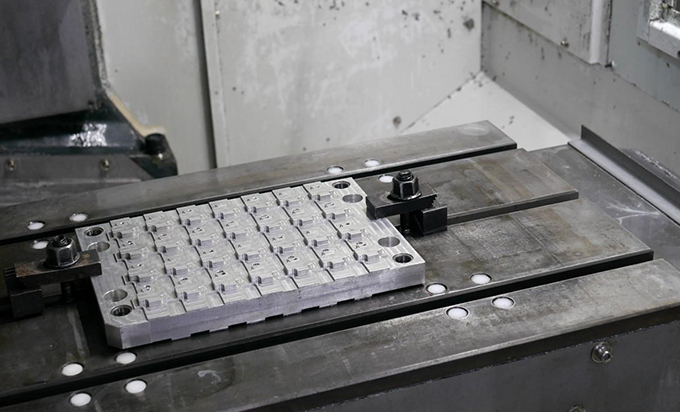
7.बाहर निकालना:
एक्सट्रूज़न एक ऐसी प्रक्रिया है जिसमें निरंतर क्रॉस-सेक्शनल आकार बनाने के लिए गर्म धातु को एक्सट्रूज़न मशीन का उपयोग करके डाई के माध्यम से मजबूर किया जाता है।मुख्य चरणों में मेटल बिलेट को पहले से गर्म करना, बाहर निकालना, ठंडा करना और काटना शामिल है।
लाभ:
कुशल उत्पादन: एक्सट्रूज़न निरंतर उत्पादन के लिए उपयुक्त है, जो लंबी लंबाई और बड़ी मात्रा में भागों के तेज़ और कुशल निर्माण को सक्षम बनाता है।
बहुमुखी आकार: एक्सट्रूज़न का उपयोग विभिन्न क्रॉस-अनुभागीय आकार, जैसे ठोस, खोखले और जटिल प्रोफाइल बनाने के लिए किया जा सकता है, जो उच्च अनुकूलनशीलता प्रदान करते हैं।
सामग्री की बचत: एक्सट्रूज़न डाई के आकार और आयामों के नियंत्रण के माध्यम से, सामग्री की बर्बादी को कम किया जा सकता है।
नुकसान:
सीमित परिशुद्धता: डाई कास्टिंग की तुलना में, एक्सट्रूज़न में कम परिशुद्धता और उच्च सतह खुरदरापन होता है।
सामग्री की सीमाएँ: एक्सट्रूज़न मुख्य रूप से एल्यूमीनियम और तांबे जैसी निंदनीय धातुओं के लिए उपयुक्त है।कठोर धातुओं के लिए यह अधिक चुनौतीपूर्ण हो जाता है।
मोल्ड विनिर्माण: एक्सट्रूज़न डाई के उत्पादन और रखरखाव के लिए विशेष कौशल की आवश्यकता होती है और उच्च लागत आती है।
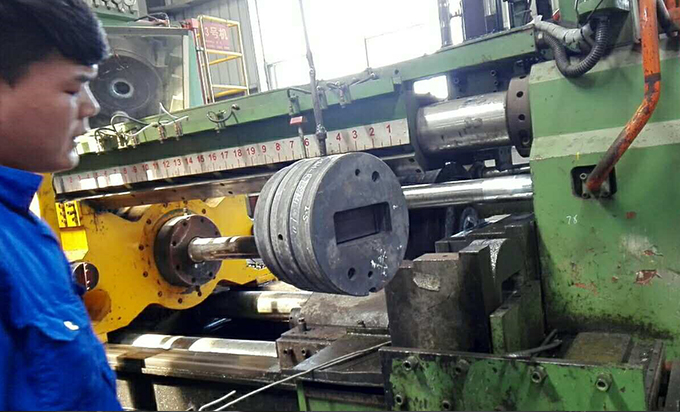
सही कस्टम धातु प्रसंस्करण विधि का चयन कैसे करें
उत्पाद डिज़ाइन और आवश्यकताएँ: आकार, आयाम, सामग्री और सतह की आवश्यकताओं सहित उत्पाद की डिज़ाइन आवश्यकताओं को समझें।विभिन्न धातु प्रसंस्करण विधियाँ विभिन्न उत्पाद डिजाइनों और आवश्यकताओं के लिए उपयुक्त हैं।
सामग्री चयन: उत्पाद की विशेषताओं और आवश्यकताओं के आधार पर उपयुक्त धातु सामग्री चुनें।विभिन्न धातु सामग्री विभिन्न प्रसंस्करण विधियों के लिए उपयुक्त हैं।उदाहरण के लिए, एल्यूमीनियम मिश्र धातु एक्सट्रूज़न और डाई कास्टिंग के लिए उपयुक्त हैं, जबकि स्टेनलेस स्टील सीएनसी मशीनिंग और कास्टिंग के लिए उपयुक्त है।
प्रसंस्करण परिशुद्धता: उत्पाद की परिशुद्धता आवश्यकताओं के आधार पर उपयुक्त प्रसंस्करण विधि का चयन करें।कुछ विधियाँ, जैसे सीएनसी मशीनिंग और ग्राइंडिंग, उच्च परिशुद्धता और सतह की गुणवत्ता प्रदान कर सकती हैं, जो उन उत्पादों के लिए उपयुक्त हैं जिन्हें उच्च सटीकता की आवश्यकता होती है।
उत्पादन की मात्रा और दक्षता: उत्पाद की उत्पादन मात्रा और दक्षता आवश्यकताओं पर विचार करें।बड़े पैमाने पर उत्पादन के लिए, स्टैम्पिंग, एक्सट्रूज़न और डाई कास्टिंग जैसी उच्च दक्षता वाली प्रसंस्करण विधियाँ अधिक उपयुक्त हो सकती हैं।छोटे-बैच उत्पादन या अनुकूलित उत्पादों के लिए, सीएनसी मशीनिंग और 3डी प्रिंटिंग जैसी विधियां लचीलापन प्रदान करती हैं।
लागत संबंधी विचार: उपकरण निवेश, प्रक्रिया प्रवाह और सामग्री लागत सहित प्रसंस्करण विधि के लागत कारकों को ध्यान में रखें।विभिन्न प्रसंस्करण विधियों में अलग-अलग लागत संरचनाएं होती हैं, इसलिए लागत-प्रभावशीलता पर विचार किया जाना चाहिए।
पेशेवर इंजीनियरों की हमारी टीम धातु प्रसंस्करण विधियों की एक विस्तृत श्रृंखला से अच्छी तरह वाकिफ है और आपको मूल्यवान अंतर्दृष्टि और सिफारिशें प्रदान कर सकती है।हमें उद्योग में नवीनतम प्रगति का गहन ज्ञान है और हम आपके विशिष्ट प्रोजेक्ट के लिए सबसे उपयुक्त विधि चुनने की जटिलताओं से निपटने में आपकी सहायता कर सकते हैं।
चाहे आपको सटीक मशीनिंग, फोर्जिंग, कास्टिंग, या किसी अन्य धातु प्रसंस्करण तकनीक में सहायता की आवश्यकता हो, हमारे इंजीनियर आपकी आवश्यकताओं के अनुरूप मार्गदर्शन प्रदान कर सकते हैं।हम आपको एक सूचित निर्णय लेने में मदद करने के लिए भौतिक गुणों, वांछित सहनशीलता, उत्पादन की मात्रा और लागत पर विचार जैसे कारकों को ध्यान में रखेंगे।
इसके अतिरिक्त, हमारे इंजीनियर विनिर्माण क्षमता के लिए आपके धातु घटकों के डिजाइन को अनुकूलित करने में सहायता प्रदान कर सकते हैं, यह सुनिश्चित करते हुए कि उन्हें चयनित प्रसंस्करण विधि का उपयोग करके कुशलतापूर्वक उत्पादित किया जा सकता है।हम डिज़ाइन संशोधनों के लिए सुझाव दे सकते हैं जो आपके उत्पादों की समग्र गुणवत्ता, कार्यक्षमता और लागत-प्रभावशीलता में सुधार कर सकते हैं।
कृपया बेझिझक मुझसे संपर्क करें और हम आपके धातुकर्म में सर्वोत्तम परिणाम प्राप्त करने में आपकी सहायता करने के लिए तैयार हैं।
पोस्ट करने का समय: दिसम्बर-18-2023