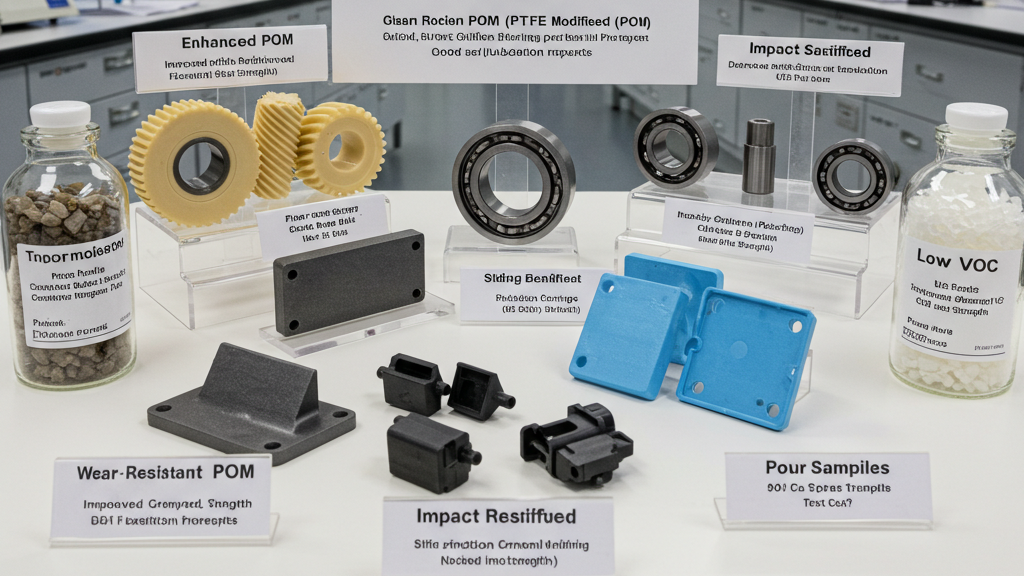
Have you ever noticed that polyoxymethylene (POM), a widely used material, has different “names”? These different names are not arbitrary and often imply differences in its performance characteristics. Understanding the meaning behind these names can help us better select and apply this material.
Having understood the different “appellations” of polyoxymethylene, how exactly do the structural differences affect actual performance? For example, what are the differences in strength, heat resistance, and other properties between homopolymer and copolymer POM? Let’s focus on these performance differences to help you clarify the application emphasis of different POM resins.
What are the main naming types of common polyoxymethylene (POM) resins?
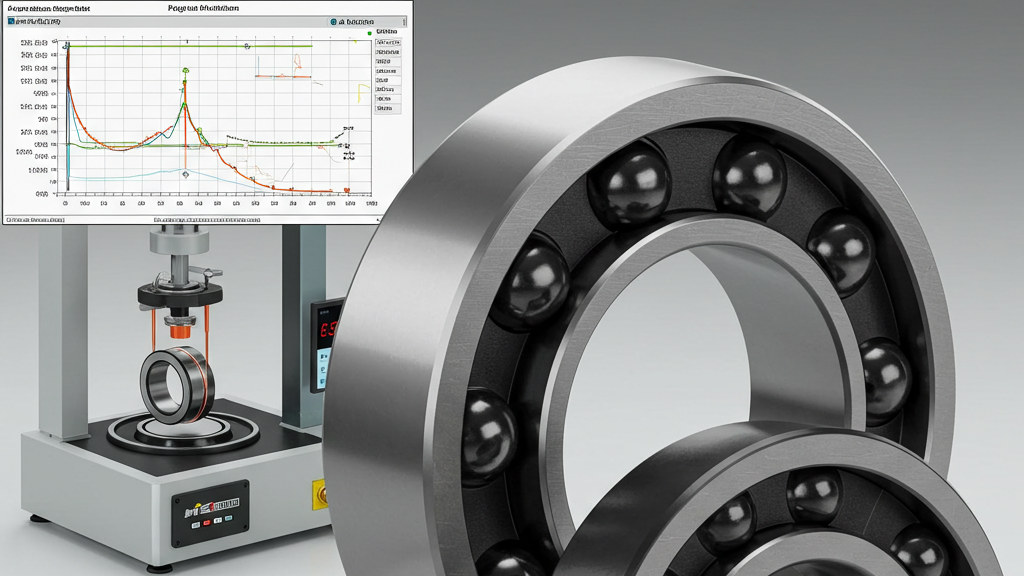
As an important engineering plastic, polyoxymethylene (POM) resin has a wide variety of “appellations” in the market. To deeply understand the differences in their performance, it is first necessary to clarify what are the main naming types of common POM resins.
- Reinforced POM: Enhanced strength and rigidity by adding fillers such as glass fiber and carbon fiber.
- Wear-Resistant POM: Improved friction performance and wear resistance by adding PTFE, graphite, etc.
- Impact-Resistant POM: Enhanced toughness by blending and modifying with other polymers.
- Low VOC POM: Models with controlled emissions of volatile organic compounds.
What are the differences in the molecular structure of POM based on different naming conventions?
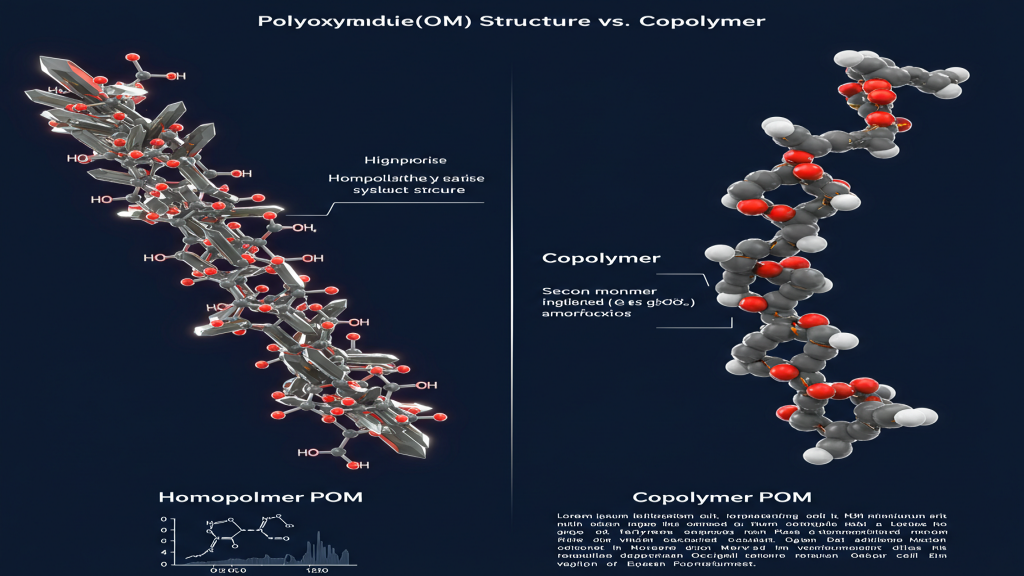
Now that we know the main naming types of polyoxymethylene, the next step is to delve into what kind of molecular structure differences are behind these different “names”. Understanding these structural differences is a crucial step in further understanding their performance differences.
- Homopolymer POM: Its molecular chain is composed of a linear repetition of single formaldehyde units, with high structural regularity and high crystallinity.
- Copolymer POM: In its molecular chain, in addition to the main formaldehyde units, a small amount of a second monomer (usually ethylene oxide or other cyclic ethers) is introduced, forming an irregular copolymer structure.
- Role of the Second Monomer: The introduced second monomer disrupts the complete regularity of the homopolymer POM molecular chain, reduces crystallinity, and thus affects the properties of the material.
- Type and Content of Comonomer: Different comonomers and their content ratio in the molecular chain will have different effects on the molecular chain structure and final performance of copolymer POM.
How does structure affect the performance of polyoxymethylene (POM)?
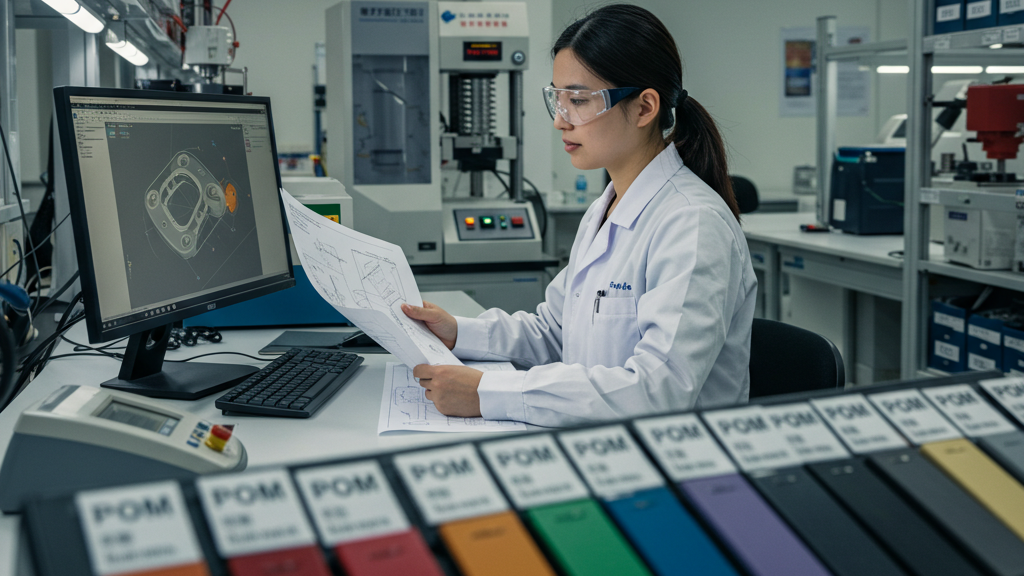
By understanding the differences in the molecular structure of differently named POM, the most crucial question then becomes: How do these seemingly small structural changes affect the performance of POM at the macroscopic level?
- Crystallinity: Homopolymer POM with high crystallinity has higher hardness, rigidity, and strength, but slightly lower toughness.
- Molecular Chain Regularity: Copolymer POM with low crystallinity has better toughness, impact resistance, and resistance to thermal oxidation.
- End-Group Stability: Copolymer POM typically has better thermal stability and chemical corrosion resistance due to the different end-group structures.
- Molecular Weight and Molecular Weight Distribution: Molecular weight and its distribution also significantly affect the processability and final performance of POM.
Performance of polyoxymethylene resin
Property |
Reinforced POM |
Wear-Resistant POM |
Impact-Modified POM |
Low VOC POM |
Strength/Stiffness | High | Medium | Medium | Medium |
Wear Resistance | Medium | High | Medium | Medium |
Impact Strength | Lower/Can be Improved | Medium | High | Medium |
VOC Emission | Medium | Medium | Medium | Low |
Main Application | Load-bearing parts | Sliding/Friction parts | Impact-resistant parts | Environmentally sensitive applications |
Selecting Polyoxymethylene (POM) Resin Based on Performance Characteristics
When selecting POM resin for practical applications, it is imperative to closely consider the end product’s usage environment and performance requirements. A thorough understanding of the performance characteristics of different modified POMs, and precisely matching them with actual application needs, is crucial to ensure the final product’s performance and reliability.
1.Choose Reinforced POM to obtain higher strength and rigidity, suitable for structural components that bear high loads.
2.Choose Wear-Resistant POM to reduce the friction coefficient and improve wear resistance, suitable for sliding parts.
3.Choose Impact-Resistant POM to enhance toughness and impact resistance, suitable for components susceptible to impact.
4.Choose Low VOC POM to reduce emissions of volatile organic compounds, suitable for applications with high environmental protection requirements.
Conclusion
The key to selecting POM resin lies in matching performance to actual needs. Choose reinforced POM for high strength, wear-resistant POM for wear resistance, impact-resistant POM for impact resistance, and low VOC POM for environmental protection. Understanding these differences will help us select the most suitable POM material for specific applications.
For expert assistance in implementing for your production needs, visit our resource center or contact us. Let’s help you scale up your manufacturing with precision and efficiency!
Post time: Apr-03-2025